Introduction
In air conditioning, heating and ventilating work, it is helpful to understand the techniques used to determine air velocity. In this field, air velocity(distance traveled per unit of time) is usually expressed in feet per minute (FPM). By multiplying air velocity by the cross section area of a duct, you can determine the air volume flowing past a point in the duct per unit of time. Volume flow is usually measured in cubic feet per minute (CFM).
Velocity or volume measurements can often be used with engineering handbook or design information to reveal proper or improper performance of an airflow system. The same principles used to determine velocity are also valuable in working with pneumatic conveying, flue gas flow and process gas systems. However, in these fields the common units of velocity and volume are sometimes different from those used in air conditioning work.
To move air, fans or blowers are usually used. They work by imparting motion and pressure to the air with either a screw propeller or paddle wheel action. When force or pressure from the fan blades causes the air to move, the moving air acquires a force or pressure component in its direction or motion due to its weight and inertia. Because of this, a flag or streamer will stand out in the air stream. This force is called velocity pressure. It is measured in inches of water column (w.c.) or water gage (w.g.). In operating duct systems, a second pressure is always present. It s independent of air velocity or movement. Known as static pressure, it act equally in all directions. In air conditioning work, this pressure is also measured in inches w.c.
In pressure or supply systems, static pressure will be positive on the discharge side of the fan. In exhaust systems, a negative static pressure will exit on the inlet side of the fan. When a fan is installed midway between the inlet and discharge of a duct system, it is normal to have a negative static pressure at the fan inlet and positive static pressure at its discharge.
Total pressure is the combination of static and velocity pressures, and is expressed in the same units. It is an important and useful concept to us because it is easy to determine and, although velocity pressure is not easy to measure directly, it can be determined easily by subtracting static pressure from total pressure. This subtraction need not be done mathematically. It can be done automatically with the instrument hook-up.
Sensing Static Pressure
For most industrial and scientific applications, the only air measurements needed are those of static pressure, total pressure and temperature. With these, air velocity and volume can be quickly calculated.
To sense static pressure, five types of devices are commonly used. These are connected with tubing to a pressure indicating instrument. Fig. 1-A shows a simple thru-wall static pressure tap. This is a sharp, burr free opening through a duct wall provided with a tubing connection of some sort on the outside. The axis of the tap or opening must be perpendicular to the direction of flow. This type of tap or sensor is used where air flow is relatively slow, smooth and without turbulence. If turbulence exists, impingement, aspiration or unequaled distribution of moving air at the opening can reduce the accuracy of readings significantly.
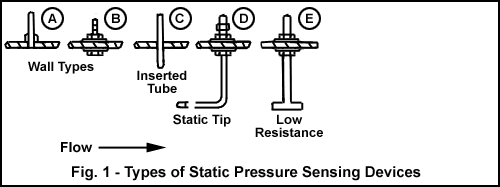
Fig. 1-B shows the Dwyer No. A-308 Static Pressure Fitting. Designed for simplified installation, it is easy to install, inexpensive, and provides accurate static pressure sensing in smooth air at velocities up to 1500 FPM.
Fig. 1-C shows a simple tube through the wall. Limitations of this type are similar to wall type 1-A.
Fig. 1-D shows a static pressure tip which is ideal for applications such as sensing the static pressure drip across industrial air filters and refrigerant coils. Here the probability of air turbulence requires that the pressure sensing openings be located away from the duct walls to minimize impingement and aspiration and thus insure accurate readings. For a permanent installation of this type, the Dwyer No. A-301 or A-302 Static Pressure Tip is used. It senses static pressure through radially-drilled holes near the tip and can be used in air flow velocities up to 12,000 FPM.
Fig. 1-E shows a Dwyer No. A-305 low resistance Static Pressure Tip. It is designed for use in dust-laden air and for rapid response applications. It is recommended where a very low actuation pressure is required for a pressure switch or indicating gage – or where response time is critical.
Measuring Total Pressure and Velocity Pressure
In sensing static pressure we make every effort to eliminate the effect of air movement. To determine velocity pressure, it is necessary to determine these effects fully and accurately. This is usually done with an impact tube which faces directly into the air stream. This type of sensor is frequently called a “total pressure pick-up” since it receives the effects of both static pressure and velocity pressure.

In Fig. 2, note that separate static connections (A) and total pressure connections (B) can be connected simultaneously across a manometer (C). Since the static pressure is applied to both sides of the manometer, its effect is canceled out and the manometer indicates only the velocity pressure.
To translate velocity pressure into actual velocity requires either mathematical calculation, reference to charts or curves, or prior calibration of the manometer to directly show velocity. In practice this type of measurement is usually made with a Pitot tube which incorporates both static and total pressure sensors in a single unit.
Essentially, a Pitot tube consists of an impact tube (which receives total pressure input) fastened concentrically inside a second tube of slightly larger diameter which receives static pressure input from radial sensing holes around the tip. The air space between inner and outer tubes permits transfer of pressure from the sensing holes to the static pressure connection at the opposite end of the Pitot tube and then, through connecting tubing, to the low or negative pressure side of a manometer. When the total pressure tube is connected to the high pressure side of the manometer, velocity pressure is indicated directly. See Fig. 3.

Since the Pitot tube is a primary standard device used to calibrate all other air velocity measuring devices, it is important that great care be taken in its design and fabrication. In modern Pitot tubes, proper nose or tip design – along with sufficient distance between nose, static pressure taps and stem – will minimize turbulence and interference. This allows use without correction or calibration factors. All Dwyer Pitot tubes are built to AMCA and ASHRAE standards and have unity calibration factors to assure accuracy.
To insure accurate velocity pressure readings, the Pitot tube tip must be pointed directly into (parallel with) the air stream. As the Pitot tube tip is parallel with the static pressure outlet tube, the latter can be used as a pointer to align the tip properly. When the Pitot tube is correctly aligned, the pressure indication will be maximum.
Because accurate readings cannot be taken in a turbulent air stream, the Pitot tube should be inserted at least 8-1/2 duct diameters downstream from elbows, bends or other obstructions which cause turbulence. To insure the most precise measurements, straightening vanes should be located 5 duct diameters upstream from the Pitot tube.
How to Take Traverse Readings
In practical situations, the velocity of the air stream is not uniform across the cross section of a duct. Friction slows the air moving close to the walls, so the velocity is greater in the center of the duct.
To obtain the average total velocity in ducts of 4″ diameter or larger, a series of velocity pressure readings must be taken at points of equal area. A formal pattern of sensing points across the duct cross section is recommended. These are known as traverse readings. Fig. 4 shows recommended Pitot tube locations for traversing round and rectangular ducts.

In round ducts, velocity pressure readings should be taken at centers of equal concentric areas. At least 20 readings should be taken along two diameters. In rectangular ducts, a minimum of 16 and a maximum of 64 readings are taken at centers of equal rectangular areas. Actual velocities for each area are calculated from individual velocity pressure readings. This allow the readings and velocities to be inspected for errors or inconsistencies. The velocities are then averaged.
By taking Pitot tube readings with extreme care, air velocity can be determined within an accuracy of ±2%. For maximum accuracy, the following precautions should be observed:
- Duct diameter should be at least 30 times the diameter of the Pitot tube.
- Located the Pitot tube section providing 8-1/2 or more duct diameters upstream and 1-1/2 or more diameters down stream of Pitot tube free of elbows, size changes or obstructions.
- Provide an egg-crate type of flow straightener 5 duct diameters upstream of Pitot tube.
- Make a complete, accurate traverse.
In small ducts or where traverse operations are otherwise impossible, an accuracy of ±5% can frequently be achieved by placing Pitot tube in center of duct. Determine velocity from the reading, then multiply by 0.9 for an approximate average.
Calculating Air Velocity from Velocity Pressure
Manometers for use with a Pitot tube are offered in a choice of two scale types. Some are made specifically for air velocity measurement and are calibrated directly in feet per minute. They are correct for standard air conditions, i.e., air density of .075 lbs. per cubic foot which corresponds to dry air at 70°F, barometric pressure of 29.92 inches Hg. To correct the velocity reading for other than standard air conditions, the actual air density must be known. It may be calculated if relative humidity, temperature and barometric pressure are known.
Most manometer scales are calibrated in inches of water. Using readings from such an instrument, the air velocity may be calculated using the basic formula:

With dry air at 29.9 inches mercury, air velocity can be read directly from the Air Velocity Flow Charts. For partially or fully saturated air a further correction is required. To save time when converting velocity pressure into air velocity, the Dwyer Air Velocity Calculator may be used. A simple slide rule, it provides for all the factors needed to calculate air velocity quickly and accurately. It is included as an accessory with each Dwyer Pitot tube.
To use the Dwyer Calculator:
- Set relative humidity on scale provided. On scale opposite known dry bulb temperature, read correction factor.
- Set temperature under barometric pressure scale. Read density of air over correction factor established in #1.
- On the other side of calculator, set air density reading just obtained on the scale provided.
- Under Pitot tube reading (velocity pressure, inches of water) read air velocity, feet per minute.
Determining Volume Flow
Once the average air velocity is know, the air flow rate in cubic feet per minute is easily computed using the formula:
Q = AV
Where: Q = Quantity of flow in cubic feet per minute.
A = Cross sectional area of duct in square feet.
V = Average velocity in feet per minute.
Determining Air Volume by Calibrated Resistance
Manufacturers of air filters, cooling and condenser coils and similar equipment often publish data from which approximate air flow can be determined. It is characteristic of such equipment to cause a pressure drop which varies proportionately to the square of the flow rate. Fig. 5 shows a typical filter and a curve for air flow versus resistance. Since it is plotted on logarithmic paper, it appears as a straight line. On this curve, a clean filter which causes a pressure drop of .50″ w.c. would indicate a flow of 2,000 CFM.

For example, assuming manufacturer’s specification for a filter, coil, etc.:
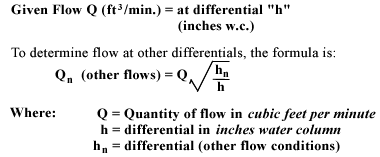
Other Devices for Measuring Air Velocity
A wide variety of devices are commercially available for measuring air velocities. These include hot wire anemometers for low air velocities, rotating and swinging vane anemometers and variable area flowmeters.
The Dwyer No. 460 Air Meter is one of the most popular and economical variable area flowmeter type anemometers. Quick and easy to use, it is a portable instrument calibrated to provide a direct reading of air velocity. A second scale is provided on the other side of the meter to read static pressure in inches w.c. The 460 Air Meter is widely used to determine air velocity and flow in ducts, and from supply and return grilles and diffusers. Two scale ranges are provided (high and low) with calibrations in both FPM and inches w.c.
To Check Accuracy
Use only devices of certified accuracy. All anemometers and to a lesser extent portable manometers should be checked regularly against a primary standard such as a hook gage or high quality micromanometer. If in doubt return your Dwyer instrument to the factory for a complete calibration check.
|